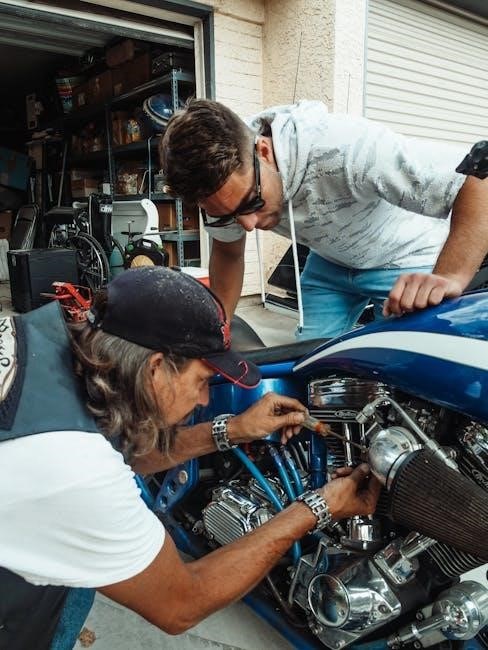
-
By:
- jayson
- No comment
dvc6200 instruction manual
The DVC6200 is a Fisher FIELDVUE digital valve controller designed for precise control in process industries. It offers advanced features, reliability, and ease of integration into automation systems.
Safety Precautions and Lockout Procedures
Always follow lockout/tagout procedures to ensure equipment remains safe during maintenance. Consult safety engineers and adhere to protocols to prevent accidental startups or energy releases.
2.1. Importance of Lockout/Tagout Procedures
Lockout/tagout procedures are essential for ensuring safety during maintenance of the DVC6200. These processes prevent accidental startups, protecting personnel from potential hazards. Proper lockout/tagout ensures all energy sources are safely controlled, minimizing risks of injury or equipment damage. Always verify that the valve is in a safe state before commencing work. Adherence to these protocols is critical to maintaining a secure working environment and complying with industrial safety standards. Regular training and updates on lockout/tagout practices are recommended to keep procedures effective and up-to-date. This ensures the safety of both the technician and the equipment.
2.2. Personal Protective Equipment (PPE) Requirements
When working with the DVC6200, proper Personal Protective Equipment (PPE) is crucial to ensure safety. This includes safety glasses, insulating gloves, and a hard hat to protect against electrical and mechanical hazards. Steel-toe boots are recommended to prevent injury from heavy objects. Additionally, avoid loose clothing that could get caught in moving parts. Always follow site-specific PPE requirements and industry standards. Proper PPE usage minimizes risks during installation, calibration, and troubleshooting. Ensure all equipment is in good condition and worn correctly. This approach helps prevent accidents and ensures compliance with safety regulations, such as those outlined by OSHA. Regular training on PPE usage is also essential.
The DVC6200 must be installed in a clean, dry environment, protected from extreme temperatures and vibrations. Mount securely to ensure proper operation and longevity. The DVC6200 must be mounted securely to a flat surface, ensuring proper alignment and levelness. Use approved hardware to prevent vibration or movement. Ensure the controller is protected from direct sunlight, moisture, and extreme temperatures. Follow torque specifications for mounting bolts to avoid damage. Install in an area with adequate ventilation to maintain operating temperatures. Use a gasket or sealant to prevent moisture ingress if installed in a humid environment. Avoid over-tightening to prevent damage to the housing. Refer to the manual for specific dimensional requirements and mounting configurations. Proper mechanical installation ensures reliable performance and longevity of the DVC6200. Always follow safety guidelines during installation. Proper wiring and electrical connections are critical for the DVC6200’s operation. Use shielded cables for communication to minimize interference. Ensure all connections are tight and secure to prevent signal loss. Follow the wiring diagram in the manual for correct terminal assignments. Verify power supply voltage matches the controller’s specifications. Use appropriate surge protection devices to safeguard against voltage spikes. Ground the controller according to the manual to prevent electrical noise and ensure safety. Avoid crossing or twisting wires to maintain signal integrity. Test all connections before powering up. Always disconnect power before making changes. Adhere to local electrical codes and safety standards during installation. Proper wiring ensures reliable communication and optimal performance of the DVC6200. The DVC6200 offers advanced control, diagnostics, and communication capabilities, enhancing valve performance in industrial processes. It integrates seamlessly with automation systems, ensuring precise operation and reliability. The DVC6200 comprises a modular design with key components such as the controller module, valve stem position sensor, and actuator interface. The controller module houses the digital electronics responsible for processing signals and executing control commands. The valve stem position sensor provides precise feedback on the valve’s position, ensuring accurate control. The actuator interface enables communication between the controller and the valve actuator, facilitating smooth operation. Additional components include communication ports for integration with external systems and status indicators for real-time monitoring. Proper understanding of these components is essential for effective installation, calibration, and troubleshooting. The DVC6200 features advanced diagnostics, real-time monitoring, and communication capabilities, enhancing operational efficiency. It supports HART and FOUNDATION Fieldbus protocols for seamless integration with modern control systems. The controller includes adaptive PID control for precise valve positioning and response. Advanced diagnostics provide detailed fault detection and predictive maintenance insights. The DVC6200 also offers explosion-proof certifications, ensuring safe operation in hazardous environments. Its robust design and intuitive software tools, such as Fisher ValveLink, simplify configuration and troubleshooting. These features make the DVC6200 a versatile and reliable solution for various industrial applications, ensuring optimal performance and safety. Its adaptability to different valve types further enhances its suitability for diverse process control needs. This section guides the calibration and configuration of the DVC6200 using tools like Fisher ValveLink software and Emerson Device Communicator for accurate setup and reliable performance. Fisher ValveLink software provides an intuitive interface for configuring the DVC6200. It allows users to set parameters, monitor performance, and troubleshoot issues. By connecting the controller to a PC, technicians can utilize the software for precise calibration, ensuring optimal valve operation. ValveLink supports advanced features like diagnostics and data logging, enhancing maintenance efficiency. Following the manual, users can easily navigate through setup, ensuring accurate and reliable configuration. This tool streamlines the process, making it accessible for both experienced professionals and those new to the DVC6200. Proper setup ensures the controller functions as intended in various industrial applications. Calibration of the DVC6200 using the Emerson Device Communicator involves specific steps to ensure accuracy. First, connect the communicator to the controller and launch the software. Select the DVC6200 from the device list and enter calibration mode. Follow the on-screen instructions to adjust settings like valve travel and response time. Once configured, verify the calibration by testing valve operation. Proper calibration ensures precise control and reliability. Refer to the instruction manual for detailed procedures, and consult the technical support checklist if issues arise. Emerson’s tools simplify the process, ensuring optimal performance tailored to your application needs. Always follow safety guidelines during calibration. Identify and resolve common issues with the DVC6200 by checking error codes, verifying wiring connections, and ensuring proper calibration. Consult the manual for detailed solutions. Diagnosing issues with the DVC6200 involves identifying error codes, checking wiring, and verifying calibration. Use the Emerson Device Communicator to review diagnostic data and troubleshoot faults. Common problems include incorrect calibration, faulty sensors, or loose connections. Begin by powering down the device and ensuring lockout/tagout procedures are in place. Consult the error code list in the manual to determine the root cause. Recalibrate the device if necessary, and verify all electrical connections are secure. If issues persist, refer to the Fisher ValveLink software for advanced troubleshooting or contact technical support for assistance. Always follow safety guidelines when performing diagnostics. The DVC6200 is supported by Emerson’s technical team, offering resources like the DVC6200 Technical Support Checklist and Fisher ValveLink software for troubleshooting and maintenance.
The DVC6200 Technical Support Checklist is a comprehensive resource available on page 80 of the instruction manual. It provides step-by-step guidance for troubleshooting and maintenance. Users can access it by referring to the manual or through Emerson’s official website. This checklist ensures that all necessary procedures are followed for optimal performance and safety. It covers calibration, configuration, and common issues, making it an essential tool for technicians and engineers. Regularly reviewing this checklist helps maintain system integrity and prevents potential operational disruptions.Installation Requirements for the DVC6200
3.1. Mechanical Installation Guidelines
3.2. Wiring and Electrical Connections
Device Overview and Key Features
4.1. Understanding the DVC6200 Components
4.2. Advanced Features of the DVC6200
Calibration and Configuration
5.1. Using Fisher ValveLink Software for Setup
5.2. Calibration Steps with Emerson Device Communicator
Troubleshooting Common Issues
6.1. Diagnosing and Resolving Operational Problems
Technical Support and Resources
7.1. Accessing the DVC6200 Technical Support Checklist