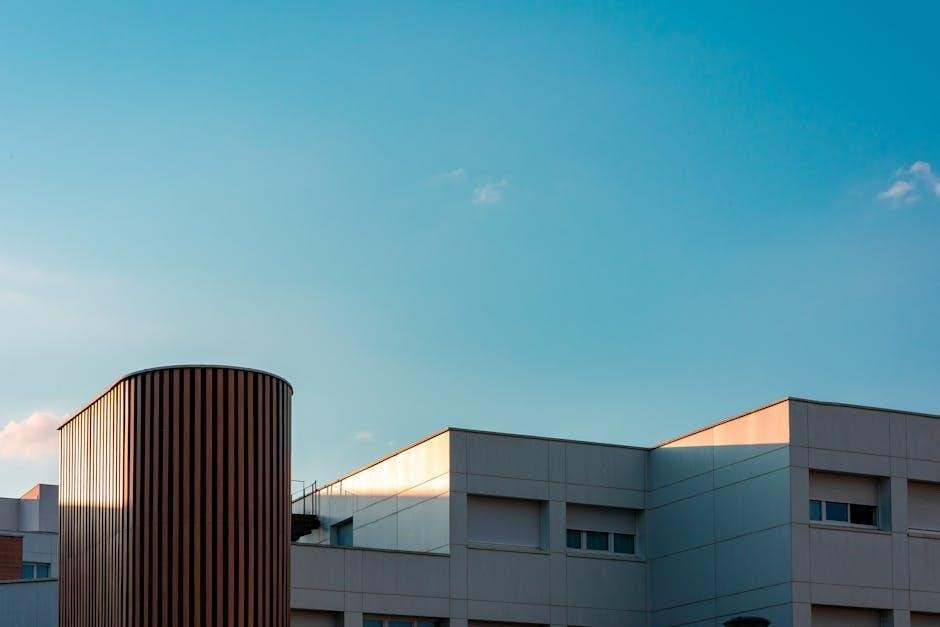
-
By:
- jayson
- No comment
9310 钢 filetype:pdf
9310 steel is a high-strength, low-alloy steel known for its durability and resistance properties, widely used in industrial and automotive applications for its exceptional performance under stress and harsh conditions․
Overview of 9310 Steel
9310 steel is a nickel-chromium alloy steel grade renowned for its high strength, toughness, and resistance to wear and fatigue․ It is classified as a low-alloy steel, making it versatile for various industrial and mechanical applications․ Known for its excellent hardenability, 9310 steel is often used in components that require high performance under stress, such as gears, axles, and shafts․ Its balanced composition ensures a combination of strength and ductility, making it suitable for both structural and dynamic loading conditions․ Additionally, 9310 steel exhibits good resistance to corrosion and heat, further enhancing its reliability in harsh environments․ Its widespread use in aerospace, automotive, and heavy machinery industries underscores its importance as a reliable and durable material․ The steel is typically heat-treated to achieve optimal properties, ensuring long service life and consistent performance in demanding applications․
Importance of 9310 Steel in Industrial Applications
9310 steel plays a critical role in industrial applications due to its exceptional strength, toughness, and resistance to wear and fatigue․ Its high hardenability and ability to withstand harsh operating conditions make it a preferred choice for manufacturing components like gears, axles, and shafts․ The steel’s durability ensures long service life in demanding environments, reducing maintenance and replacement costs․ Its versatility allows it to be used in various industries, including aerospace, automotive, and heavy machinery, where reliability under stress is paramount․ Additionally, 9310 steel’s resistance to corrosion and heat further enhances its suitability for applications in challenging settings․ Its balanced properties of strength and ductility make it ideal for both structural and dynamic loading conditions, ensuring consistent performance and safety․ As a result, 9310 steel is indispensable in industries requiring high-performance materials to meet rigorous operational demands․
Chemical Composition of 9310 Steel
9310 steel is primarily composed of iron, with key alloying elements including nickel (1․0-1․4%), chromium (0․5-1․0%), manganese (0․3-0․7%), silicon (0․1-0․3%), and carbon (0․1%)․
Key Elements in 9310 Steel
9310 steel contains a balanced mix of alloying elements that enhance its mechanical properties․ Nickel (1․0-1․4%) is a primary component, contributing to toughness and resistance to wear․ Chromium (0․5-1․0%) enhances hardness and corrosion resistance, while manganese (0․3-0․7%) improves strength and hardness․ Carbon (0․1%) is present to increase hardness, and silicon (0․1-0․3%) strengthens the steel matrix․ Additionally, molybdenum (0․1-0․2%) is added to improve high-temperature stability and resistance to deformation․ These elements work synergistically to achieve the desired properties for industrial and automotive applications, ensuring durability and performance under stress․ The precise balance of these elements is critical to maintaining the steel’s versatility and reliability in demanding environments․
Effect of Alloying Elements on Properties
The alloying elements in 9310 steel significantly influence its mechanical and physical properties․ Nickel enhances toughness and resistance to wear, while chromium improves hardness and corrosion resistance․ Manganese contributes to strength and hardness, and carbon boosts hardness and wear resistance․ Silicon strengthens the steel matrix, and molybdenum improves high-temperature stability and resistance to deformation․ These elements collectively enhance the steel’s strength, durability, and resistance to environmental factors, making it suitable for demanding applications․ The combination of these elements ensures that 9310 steel exhibits excellent fatigue resistance, high strength, and resistance to wear and corrosion, making it a reliable choice for industrial and automotive components․ The balanced composition ensures optimal performance under stress and harsh operating conditions, while maintaining ductility and ease of machining․
Physical and Mechanical Properties
9310 steel exhibits exceptional strength, hardness, and toughness, combined with high resistance to fatigue, wear, and corrosion, making it ideal for demanding industrial and automotive applications requiring durability and reliability․
Strength and Hardness of 9310 Steel
9310 steel is renowned for its exceptional strength and hardness, making it a preferred choice for high-performance applications; Its ultimate tensile strength ranges between 180,000 and 200,000 psi, while its yield strength is approximately 150,000 psi․ The steel achieves a Rockwell hardness of around 55 HRC after heat treatment, ensuring superior resistance to wear and deformation․ Its high strength-to-weight ratio allows it to withstand heavy loads without compromising on durability․ The combination of strength and hardness makes 9310 steel ideal for components like gears, axles, and other critical machinery parts that require both rigidity and toughness․ Its ability to maintain structural integrity under extreme stress is a key factor in its widespread use across industries․
- Tensile strength: 180,000–200,000 psi
- Yield strength: ~150,000 psi
- Rockwell hardness: ~55 HRC
Durability and Resistance Characteristics
9310 steel exhibits outstanding durability and resistance properties, making it highly suitable for demanding industrial and automotive applications․ It offers excellent fatigue strength, with a fatigue limit of approximately 70,000 psi, ensuring long-term reliability under cyclic loading conditions․ The steel also demonstrates superior resistance to wear and abrasion, particularly after heat treatment, which enhances its surface hardness․ Additionally, 9310 steel possesses good corrosion resistance in non-severe environments and maintains its structural integrity at elevated temperatures․ Its ability to withstand high stress and dynamic loads without premature failure is a testament to its robustness․ These characteristics make it an ideal material for critical components such as gears, axles, and shafts, where durability and resistance to degradation are paramount․
- Fatigue limit: ~70,000 psi
- Wear resistance: Enhanced after heat treatment
- Corrosion resistance: Suitable for non-severe environments
Manufacturing Process of 9310 Steel
9310 steel’s manufacturing involves precise production steps and stringent quality control to ensure optimal material properties and performance․ Adherence to industry standards is critical during its creation for reliable industrial applications․
Production Steps for 9310 Steel
The production of 9310 steel involves several critical steps to ensure its high-quality properties․ First, raw materials are selected and melted in an electric arc furnace to achieve the desired chemical composition․ The molten steel is then cast into ingots or continuously cast into slabs․ Next, the steel undergoes hot rolling to shape it into the required form, such as bars or sheets․ Heat treatment, including annealing, normalizing, and tempering, is applied to enhance mechanical properties like strength and toughness․ Finally, the steel is subjected to rigorous quality control tests, including hardness checks, tensile testing, and non-destructive inspections, to ensure it meets industry standards for performance and reliability․
Quality Control Measures in Manufacturing
The manufacturing of 9310 steel involves stringent quality control measures to ensure consistency and reliability․ Spectroscopy is used to verify the chemical composition, while mechanical testing, such as tensile and hardness tests, confirms the steel’s strength and durability․ Non-destructive testing, including ultrasonic and magnetic particle inspections, detects any internal or surface defects․ Dimensional checks are performed to ensure compliance with specified tolerances․ Heat treatment processes are closely monitored to achieve the desired microstructure and properties․ Documentation and traceability are maintained throughout production to meet certification standards․ Regular audits and inspections are conducted to ensure adherence to industry norms․ The combination of advanced testing techniques and rigorous oversight guarantees that 9310 steel meets the highest performance and safety requirements for its intended applications․